Entwickeln mit System - am digitalen Zwilling
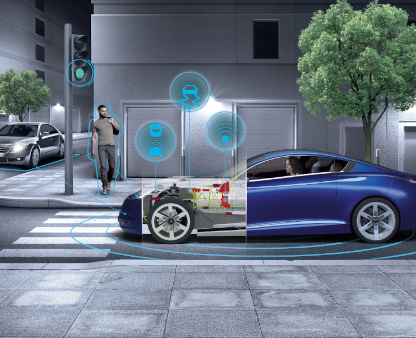
Das komplexe Zusammenspiel von Mechanik, Elektronik und Software – mit Systems Engineering den Überblick behalten um den digitalen Zwilling zu erschaffen.
Ob in der Waschmaschine oder im Auto – Systems Engineering verbindet die Disziplinen Mechanik, Elektrik/Elektronik und Software. Mit einer ganzheitlichen Entwicklungsplattform lässt sich der Überblick wahren. Das Prinzip hat sich in der Luftfahrt und der Automobilindustrie bereits durchgesetzt. Jetzt erkennt auch der Anlagen- und Maschinenbau die Vorteile.
Die Kofferraumklappe schließt nicht, der Stoffzipfel des Mantels hat sich in der Schließe verfangen. Die elektrische Klappe schwingt wieder auf, damit der Fahrer den Mantel richtig im Kofferraum verstauen kann. Sollte sie zumindest.
Aber heute liegt eine dicke Schneeschicht auf dem Wagen und der kleine Elektromotor schafft es nicht, die Last anzuheben. Ein Antrieb mit Lastsensor und variabler Kraft sollte die Klappe eigentlich korrekt öffnen – doch das Zusammenspiel aus Elektrik und Mechanik funktioniert nicht optimal.
Ein Beispiel für viele meistens harmlose, manchmal aber auch gefährliche Ärgernisse und Fehler, mit denen wir uns herumschlagen müssen. Ob eine Heckklappe nicht richtig schließt oder ob eine Rakete explodiert, ist von den Folgen ein großer Unterschied – die Ursache ist oft die gleiche: Mangelnde Koordination verschiedener Ingenieure, etwa von Hardware und Software-Entwicklern. Steuergeräte für komplexe Funktionen, beispielsweise in einem Auto, führen hunderte mechanische und elektrische Funktionen aus. Bei ihrer Entwicklung müssten die Fachdisziplinen, die in Unternehmen oft noch in Abteilungen getrennt sind, Hand in Hand arbeiten und das am selben digitalen Modell.
Entwicklung ganzheitlich denken
Hier setzt Systems Engineering an. Der Begriff wurde bereits in den 1940er Jahren in den USA geprägt, seit den 1970ern wird er auch in Deutschland verwendet. Unter Systems Engineering versteht man heute einen ganzheitlichen Entwicklungsprozess, bei dem alle Schritte von der Definition der Anforderungen bis zum fertigen Produkt und sogar bis zur Vermarktung und zum Recycling von Anfang an mitbedacht und mitgeplant werden.
Beschäftigten sich Ingenieure früher hauptsächlich mit der Frage „Was will ich entwickeln?“, lenkt Systems Engineering den Blick auf die Frage „Wie will ich es entwickeln?“, der Entwicklungsprozess wird zum erfolgskritischen Faktor für das künftige Produkt. Auch das berüchtigte Bermuda-Dreieck aus Mechanik, Elektronik und Software, in dem Entwicklungsprojekte leicht Schiffbruch erleiden, kann Systems Engineering überwinden.
Voraussetzung dafür ist die vollständige Digitalisierung des Entwicklungsprozesses und eine Vereinheitlichung der Entwicklungsdaten. Jeder Ingenieur – idealerweise auch bei den Zulieferern – arbeitet jederzeit am aktuellsten Datensatz. Ändert sich die mechanische Konstruktion, hat das direkte Auswirkungen auf die Steuerung. Und eine Simulation klärt, ob alles wie gewünscht funktioniert. Systems Engineering verkürzt Entwicklungsprozesse deutlich, spart Kosten und vermeidet Fehler schon im Ansatz.
Kluft zwischen Theorie und Praxis
Soweit die Theorie. In der Praxis ist Systems Engineering in Reinkultur noch wenig verbreitet. Der Ansatz, aus den Anforderungen ein digitales Modell zu entwickeln und zu testen und erst dann in ein physisches Pendant zu übersetzen, ist zwar anerkannt, wird aber nicht immer effizient gelebt. Zum Teil tauschen die Entwickler zwischen verschiedenen Abteilungen oder Unternehmen eines Wertschöpfungsnetzwerks Informationen mittels Word- oder Excel-Dateien aus, die dann in die CAD/PLM-Software eingepflegt wird. Dabei passieren Fehler. Manchmal erfüllt das fertige Produkt nicht alle Anforderungen, die in der Designphase definiert wurden. Und manchmal erfüllt es Anforderungen, die überhaupt nicht erwünscht waren. „Mitunter verlieren Entwickler einfach den Überblick“, so ein Experte für Systems Engineering bei Dassault Systèmes.
Der Aufbau von strategischen Partnerschaften spielt eine wesentliche Rolle. Daher hat Dassault Systèmes beispielsweise mit Partnern aus der Wissenschaft die Fachgruppe Systems Engineering im Spitzencluster „Intelligente Technische Systeme Ostwestfalen-Lippe“ (it’s OWL) in Paderborn gegründet. In dem Cluster haben sich Unternehmen, Universitäten und weitere Partner zusammengeschlossen, die sich mit der Entwicklung und Produktion der Zukunft unter dem Oberbegriff Industrie 4.0 befassen.
Das Heinz Nixdorf Institut und das Fraunhofer-Institut für Produktionstechnologie, beide Mitglieder von it´s OWL, haben 2013 in der Studie „Systems Engineering in der industriellen Praxis“ festgestellt, dass Unternehmen die wachsende Interdisziplinarität als größte Herausforderung im Produkt- Engineering ansehen. Treiber seien intelligente Produkte und cyberphysische Systeme im Gefolge von Industrie 4.0. Systems Engineering könne helfen, die Herausforderungen zu bewältigen, doch müsse der Nachweis des Nutzens noch deutlicher werden.
Ein Modell für Alle
Die hohe Schule ist das modellbasierte Systems Engineering (MBSE), das für die Entwicklung komplexer und intelligenter Systeme immer wichtiger wird. Mit „Modell“ ist hier nicht allein das optische Design gemeint, das man in einem CAD-Programm entwirft. Das Modell enthält vielmehr alle Anforderungen und Spezifikationen für das spätere Produkt und koordiniert den gesamten Lebenszyklus eines Produkts, darunter auch Qualitätstests und Anforderungen ans Recycling. MBSE setzt voraus, dass es genau eine digitale Repräsentanz des Projekts gibt, an dem alle Beteiligten in einem Entwicklungsprozess arbeiten. Kommt es zu Änderungen, ist das sofort für alle sichtbar. Das spart Rückkopplungsschleifen und damit Zeit und Geld. Für das Eingangsbeispiel würde das bedeuten: Die gesamte mechatronische Auslegung des Heckklappenantriebs erfolgt aus einem Guss. Alle Anwendungsfälle – zum Beispiel mit Schnee oder ohne – werden in einem Schritt in Hard- und Software modelliert.
Transparenz und Kostenersparnis
Wieviel Zeit und Geld man damit genau spart, lässt sich schwer beziffern, dazu ist Systems Engineering in seiner heutigen Bedeutung noch zu neu, es wird auch nicht schlagartig, sondern eher über Jahre in einem evolutionären Prozess eingeführt. Die Hoffnung ist, dass Automobilhersteller künftig weniger Rückrufaktionen haben werden. Und wenn es doch zu Störungen kommt, kann die Ursache wesentlich schneller aufgespürt werden. Denn Systems Engineering dokumentiert jeden Schritt des Entwicklungsprozesses, es ist eine Art Gedächtnis für spätere Generationen von Entwicklern.
Vorreiter beim Systems Engineering ist die Luftfahrtindustrie. Früher umfasste das „Handbuch“ eines Passagierflugzeugs einen Kubikmeter Papier. Das zeigt, wie komplex die Entwicklung eines Jets ist. Kaum weniger anspruchsvoll ist die Entwicklung eines Automobils. Neue Fahrzeuge sind Computer auf Rädern mit Dutzenden Assistenzsystemen vom Abstandsradar bis zur Klimatisierung. Millionen Zeilen Softwarecode überwachen und steuern das Fahrzeug, gleichzeitig wächst die mechanische Komplexität dank Sitzverstellung und elektrischer Kofferraumklappe. Kein Wunder, dass die Automobilindustrie sehr an Systems Engineering interessiert ist.
Aber auch viele weitere Branchen profitieren davon, insbesondere Unternehmen aus dem Mittelstand. So hat das Cluster in Paderborn mit Kannegiesser, einem Hersteller von Waschmaschinen für Großwäschereien, die gesamte Prozesskette optimiert. Eine Anlage von der Größe eines Fußballfeldes verarbeitet 50 Tonnen Wäsche pro Tag, meist aus Krankenhäusern, und verbraucht dabei zwei Tonnen Waschmittel. Mit Prinzipien des Systems Engineering haben die Wissenschaftler des Clusters die Wäsche und den gesamten Prozess in einem Modell simuliert. Der Lohn: eine selbstoptimierende Waschmaschine, die den Verbrauch von Wasser und Waschmittel verringert und die Hygiene der Wäsche durch Einsatz von Robotern verbessert.
3DEXPERIENCE in der Entwicklung
Mit dem Zusammenwachsen von Mechanik, Elektrik/Elektronik und Software müssen auch die Entwurfswerkzeuge zusammenwachsen. Dassault Systèmes ist hier mit seiner 3DEXPERIENCE Plattform Vorreiter. In ihr verschmelzen einst getrennte Softwarelösungen wie das bekannte CAD-Programm CATIA oder SIMULIA, ein Simulationsprogramm für Produktentwicklung und -test. Ziel ist eine virtuelle Welt, in der Entwickler ihre Produkte lebensnah entwickeln und auf Herz und Nieren prüfen können. Im Rechner schwingt die Heckklappe eines Autos tausendmal auf und zu, lange bevor die Produktion anläuft. Die Entwicklung folgt dem RFLP-Konzept: Es definiert die Anforderungen (Requirements), die Funktionsarchitektur (Functional), die logische Ebene (Logical) in 2D und 3D sowie die physikalische Ebene (Physical). Erst dann erfolgt die Umsetzung in ein physisches Produkt.
Weil Systems Engineering für kleine und mittelständische Unternehmen auf den ersten Blick recht abstrakt wirkt, haben die Partner der Fachgruppe in Paderborn im Mai 2017 das Engineering Collaboration Lab (E-Co-Lab) eingerichtet. Dort können Unternehmen die Möglichkeiten von Systems Engineering und der 3DEXPERIENCE Plattform an konkreten Beispielen testen.
Offen für Alle
Voraussetzung für Systems Engineering ist, dass alle Datenquellen, Standards und Softwaretools in einem Unternehmen nahtlos in einer Plattform zusammenspielen. Dassault Systèmes unterstützt hier den Codex of PLM Openness, bei dem es sich um eine von Automobil-OEMs, Lieferanten und dem ProSTEP iViP Verein vorangetriebene Initiative handelt. So ist die Webservice-Infrastruktur der 3DEXPERIENCE Plattform mit zahlreichen Schnittstellenstandards kompatibel. Unterstützt werden auch viele Austauschformate wie STEP, IGES, Modelica, FMI, AUTOSAR und JT, um eine Offenheit nach außen hin zu gewährleisten. Die Automobilindustrie setzt bisher hunderte spezialisierte Softwaretools für verschiedene Entwicklungsaufgaben ein.
Gleichzeitig baut Dassault Systèmes seine 3DEXPERIENCE Plattform weiter aus, sowohl durch eigene Entwicklungen als auch durch gezielte Technologie-Akquisitionen wie Dymola zur Modellierung und Simulation mechatronischer Systeme, Reqtify für die Anforderungsnachverfolgung oder Safety Designer zur Auswirkungs- und Fehlerbaumanalyse.
Die 3DEXPERIENCE Plattform bildet die Grundlage unserer in 12 Branchen eingesetzten Anwendungen und bietet ein breites Portfolio von Branchenlösungen. Dassault Systèmes, "The 3DEXPERIENCE Company", ermöglicht Unternehmen und Menschen durch virtuelle Welten, nachhaltige Innovationen tatsächlich erlebbar zu machen. Seine weltweit führenden Lösungen verändern die Art und Weise, Produkte zu entwickeln, zu produzieren und zu warten. Die Lösungen von Dassault Systèmes fördern die soziale Innovation und erweitern damit die Möglichkeiten für die virtuelle Welt, die reale Welt zu verbessern. Der Konzern bringt Mehrwert für über 220.000 Kunden jeder Größe und in allen Branchen in mehr als 140 Ländern. Weitere Informationen erhalten Sie unter www.3ds.com/de.
Weitere Informationen erhalten Sie unter unserem Freecall: 0800-3DEXPERience (-3339737)